Solutions
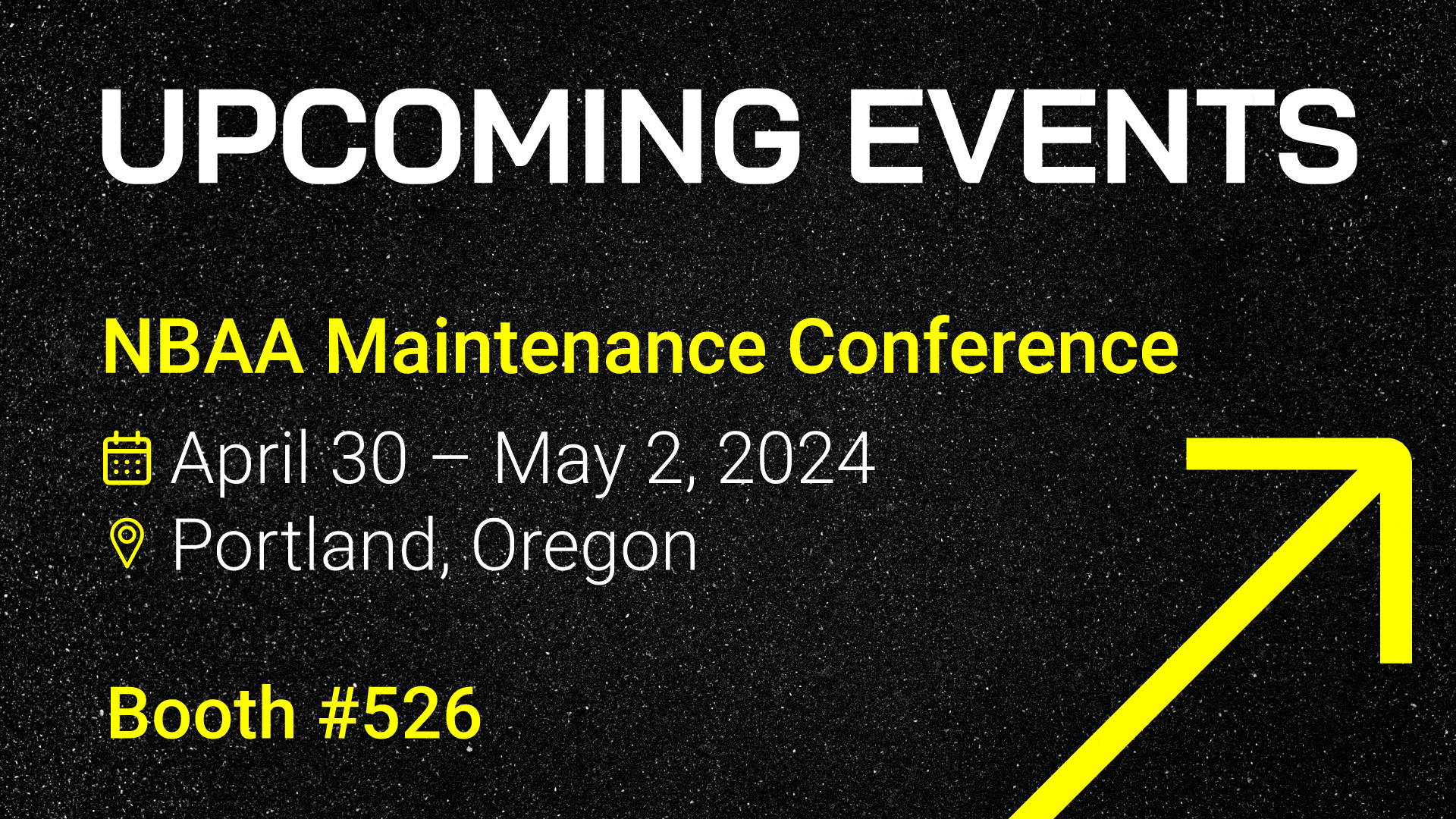
Meet Veryon at industry events
Come meet the Veryon team and see our solutions in action.
Products
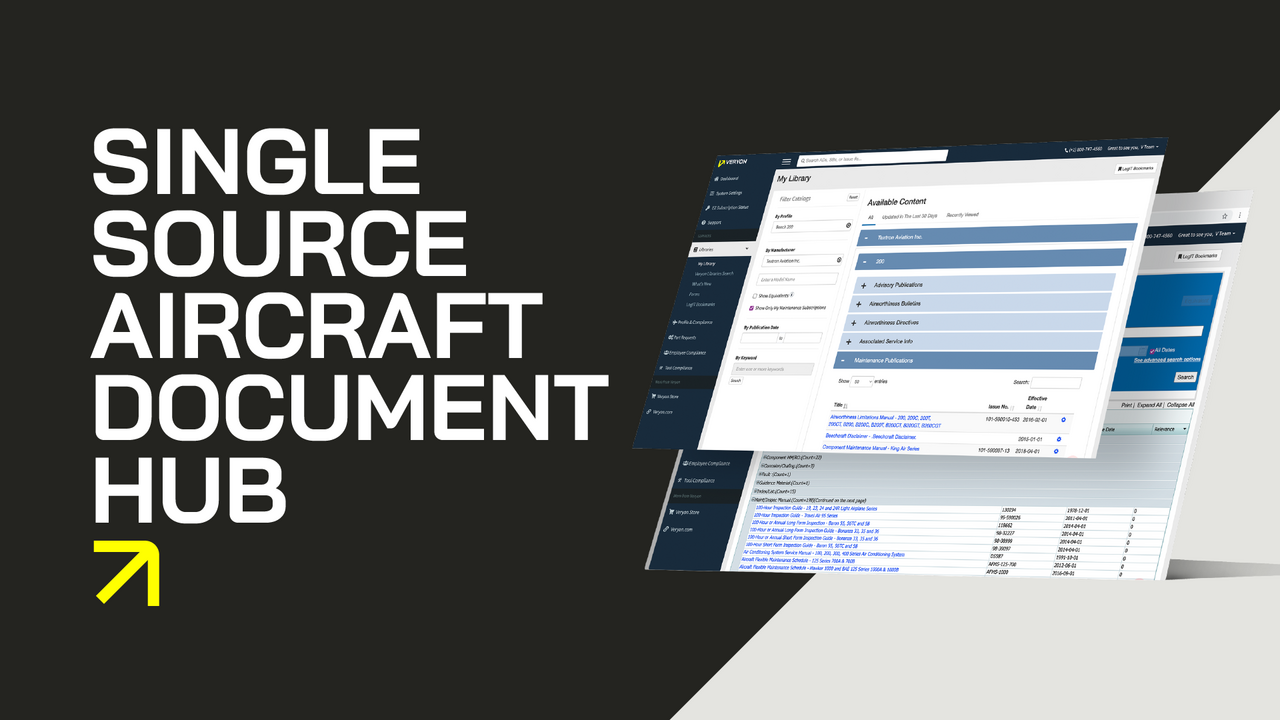
Discover Veryon Publications
Access your aircraft maintenance manuals and regulatory publications all in one place.
Resources

Join us at the NBAA Maintenance Conference
Swing by booth #526 to get a free t-shirt and a chance to win a Yeti Cooler.
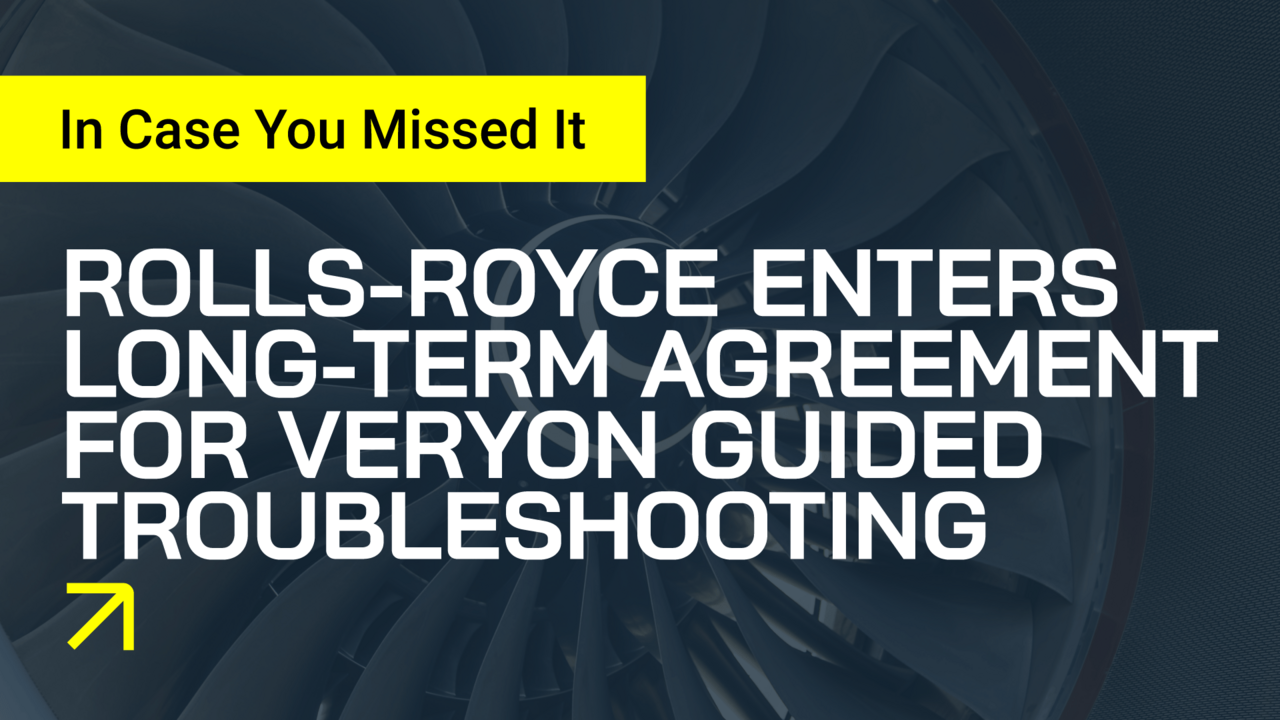
Rolls-Royce Deutschland expands partnership with Veryon
The world's leading engine supplier in Business Aviation has signed a long-term agreement for Veryon's Guided Troubleshooting product.
How HAECO INCREASED OVERSIGHT
OF MAINTENANCE ACTIVITIES
WITH VERYON TRACKING+
Veryon Tracking+ (formerly Rusada ENVISION) has revolutionized HAECO's
visibility into maintenance tracking, making their operations more
efficient than ever.
About the customer
HAECO is one of the leading independent MRO service providers in the aviation industry, providing a comprehensive range of products and services in the Airframe, Cabin, Component, and Engine segments through its 16 operating companies worldwide.
Its Engine Services division provides engine MRO and component repair services from Hong Kong, Xiamen, Dallas, and Amsterdam.
Headquarters
Lantau, Hong Kong
Founded
1950
Company size
13,000+
The challenge
HACECO's main challenge was the labor-intensive manual work of planning and reviewing maintenance projects. Management had to review documents one by one before seeking out HAECO team members for reviews and progress updates. Without a single source of truth, there were redundant workflows, and issues with inventory management.
The outcome
The implementation of Veryon Tracking+ brought significant benefits to HAECO's maintenance operations. They were able to generate dashboards to show management the progress of jobs and the status of key performance indicators. With their inventory and transactions being tracked digitally, they reduced their stock. Instead of spending hours updating and reviewing paperwork with individual team members, HAECO can operate more efficiently than ever with improved training and visibility across its operations.
"As well as improving our visibility and planning capabilities, Veryon Tracking+ significantly reduced paperwork as all actions were tracked in the system, and digital copies of documents were stored against respective transactions. This was a key objective for the project and has resulted in increased efficiency throughout our operations."
Julian Potter | HAECO Global Engine Support
Detecting the undetected issues
Upon implementing Veryon Tracking+, HAECO experienced smoother planning and could use one view to report on several projects at once.
Working in a fast-paced environment can make picking up the little details difficult. Intelligent platforms like Veryon Tracking+ can help MRO leaders make quick and effective decisions.
Saving time and improving uptime
The HAECO team observed significant time savings and increased aircraft uptime after integrating Veryon Tracking+, achieved through the following key benefits:
-
Optimized Workflows and Reduced Redundancy: Veryon streamlined maintenance processes by efficiently eliminating redundant approaches, resulting in valuable time and resource savings. It enabled the team to address issues in a structured and efficient manner.
-
Intuitive User Interface: Team members commended Veryon for its user-friendly interface, making it easily adaptable. The intuitive design facilitated accessibility for personnel with varying technical expertise, enhancing overall usability.
-
Potential for Mobile Accessibility: While not yet fully implemented, the team recognized the value of mobile accessibility for line maintenance staff.
Customer support and onboarding experience
The HAECO team was very satisfied with the customer onboarding process and support, participating in regular onsite support trainings. During onboarding, the Veryon team worked closely with maintenance planning staff, engineers, supervisors, and maintenance control personnel to ensure they could seamlessly integrate the system into their maintenance operations.
Summary
In conclusion, Veryon Tracking+ has significantly improved HAECO's maintenance oversight, saving considerable money and time. By implementing Veryon Tracking+, they were able to:
- Improve Maintenance Projects: Veryon Tracking+ streamlines processes and uses intelligent planning to help you reduce turnaround times and increase productivity.
- Enhance Inventory Management: Veryon's interfacing abilities allowed for a direct link between HAECO’s in-house ‘ECHO’ and Tracking+, which enabled inventory to flow smoothly between the two systems.
- Efficient People Management: The system's ability to provide support for HAECO's business activities like HR allows the team to get the most out of their workforce through effective employee management.
Resources
© 2024 Veryon all rights reserved.